A: Selecting the proper mirror for laser system requires consideration of a number of factors, including reflectivity, laser damage resistance, coating durability, thermal expansion of the substrate, wavefront distortion, scattered light, and cost. These mirror characteristics depend on the optical coating, the substrate, and the surface quality. The optical coating is the most critical component of a mirror as it dictates its reflectivity and durability. Optical mirror coatings are typically made up of either metallic or dielectric materials. By virtue of their conductivity, metals have a complex index of refraction with a large imaginary part over a very wide wavelength range. This gives rise to a large reflectivity that is relatively insensitive to wavelength, which gives metallic mirrors their shiny appearance. Metallic coatings are usually made of silver, gold, or aluminum and the resulting mirrors can be used over a very broad spectral range (see figure 3). Metallic coatings are relatively soft, making them susceptible to damage, and special care must be taken when cleaning. Mirrors with dielectric coatings are more durable, easier to clean, and more resistant to laser damage. However, as a consequence of their dispersive and predominantly real indices of refraction, dielectric mirrors have a narrower spectral reflectivity and are typically used in the VIS and NIR spectral region. There is greater flexibility in the design of dielectric coatings compared to metallic coatings. When compared with metallic mirrors, a dielectric mirror can offer higher reflectivity over certain spectral ranges and can offer a tailored spectral response (see figure 3).
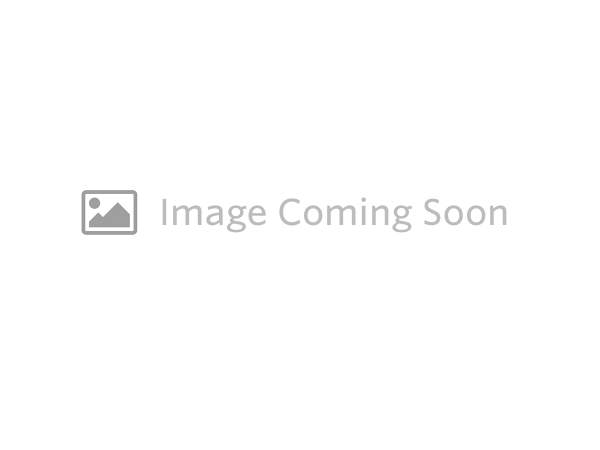
Figure 3. Reflection spectra of silver metallic mirrors showing broadband reflectivity (left) and dielectric laser-line mirror showing two narrow reflection bands (right).
Most substrates upon which the coatings are deposited are dielectric materials and these substrates control the thermal expansion and transmission properties of mirrors. Certain materials have lower thermal expansion coefficients, e.g., fused silica, than others, e.g. N-BK7 optical glass, but the cost of the material and ease of polishing must also be considered. If light transmitted through the substrate is not required, the backside of the substrate is typically ground to prevent inadvertent transmissions. However, for transmissive mirrors, a substrate material with a homogenous index of refraction is important, e.g. fused silica.
Prior to depositing the optical coating, the substrate's surface must be ground and polished to the proper shape (either planar or curved). The surface quality and flatness determine the fidelity of the mirror performance with the targeted application dictating the requirements for these parameters. Surface flatness is often specified in wavelengths, e.g. λ/10, over the entire usable area of the mirror. When preservation of the wave front is critical, a λ/10 to λ/20 mirror should be selected, while less demanding applications can tolerate a λ/2 to λ/5 mirror with the associated reduction in cost. Surface quality is usually dictated by the severity of random localized defects on the surface. These are often quantified in terms of a "scratch and dig" specification, e.g. 20-10, with a lower value indicating improved quality and therefore lower scattering. For high precision surfaces, such as those found within the cavity of a laser, a scratch-dig specification of 10-5 may be required since it would yield very little scattered light.
Surface polishing tolerances in terms of irregularity, surface roughness, and cosmetic imperfections are verified using state-of-the-art metrology equipment. These same parameters and procedures are used to assess the quality and flatness of other optical components such as lenses or windows.